A master potter’s journey: 40 years of crafting tradition in Avanos
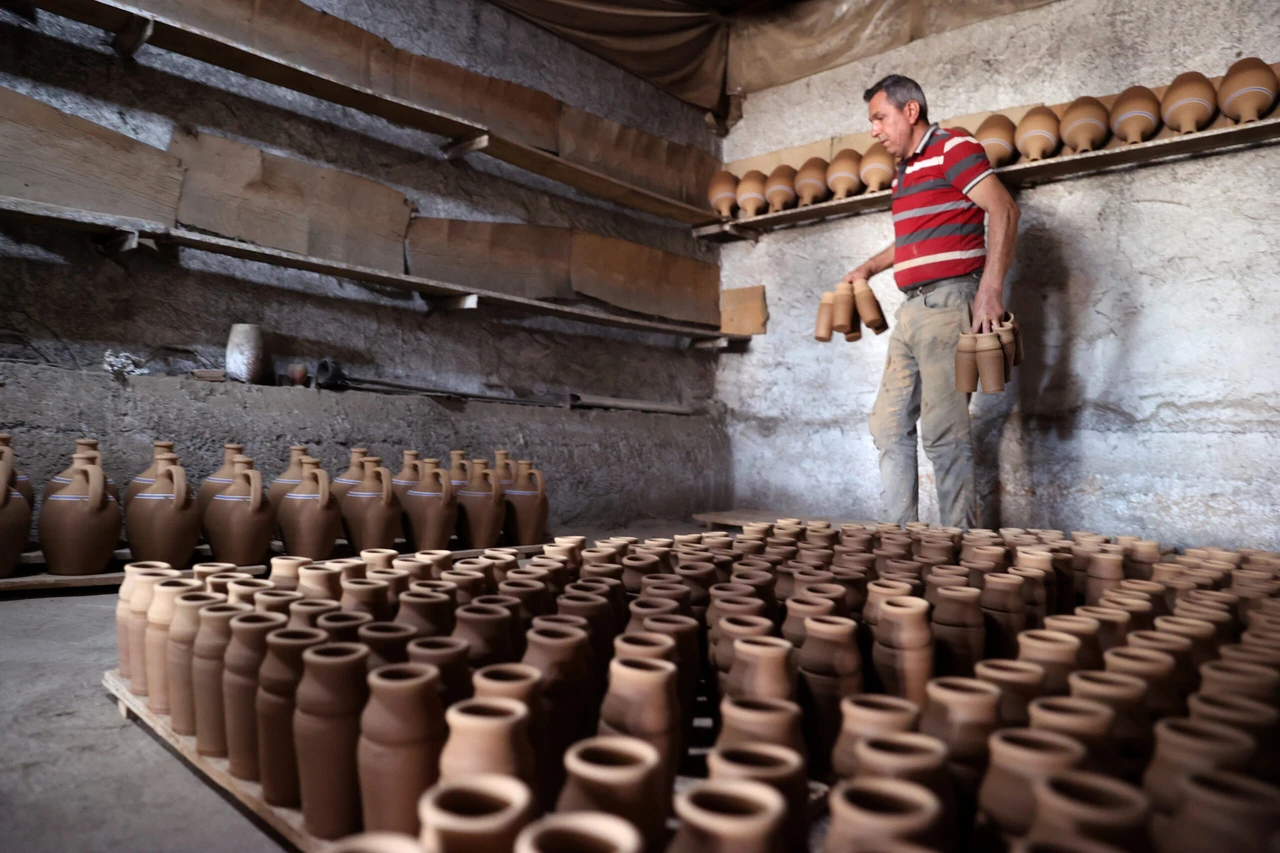
In the heart of Cappadocia’s Avanos district, 56-year-old Hakan Hakki Col stands as a testament to the enduring legacy of pottery. Having honed his craft from a tender age in his grandfather’s workshop, Col has spent over four decades mastering the art of shaping clay on a traditional wheel.
Pottery in Avanos traces its origins back approximately 4,000 years to the Hittite period. This ancient craft has been handed down through generations, and today, it remains a vital part of the region’s cultural and economic fabric.
Avanos, a favorite destination for both local and foreign tourists visiting Cappadocia, boasts a vibrant community of artisans who continue to produce pottery using age-old techniques.
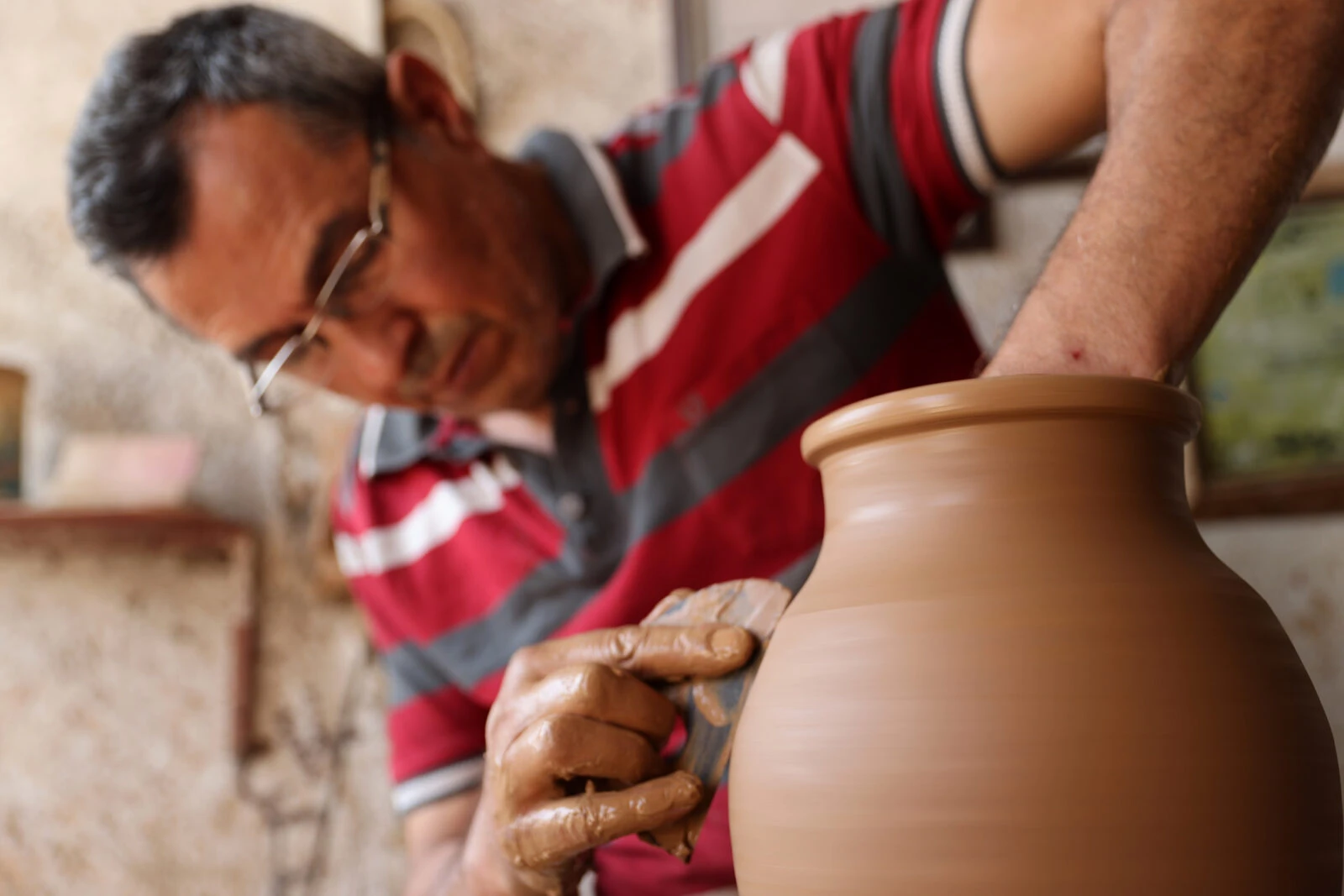
Master potter from a young age
Col’s journey began long before he attended primary school. At just six years old, he earned the title of apprentice in his grandfather’s workshop and ascended to master status by the age of 16. Despite the advent of modern technology, Col remains committed to traditional methods, crafting iconic local items such as testis and cheese pots by hand.
Each piece he produces reflects the dedication and care of a true artisan.
Passion beyond retirement
Even after retiring two years ago, Col cannot resist the allure of his wheel. “The smell of the workshop is unique and brings peace when you enter. We love our job. If we didn’t love it, we wouldn’t be working at this age,” he says.
His day begins with preparing the clay, continuing a family tradition that spans generations. His grandfather and father were also potters, and Col has worked tirelessly to keep the family workshop alive, adapting to the evolving demands of tourism.
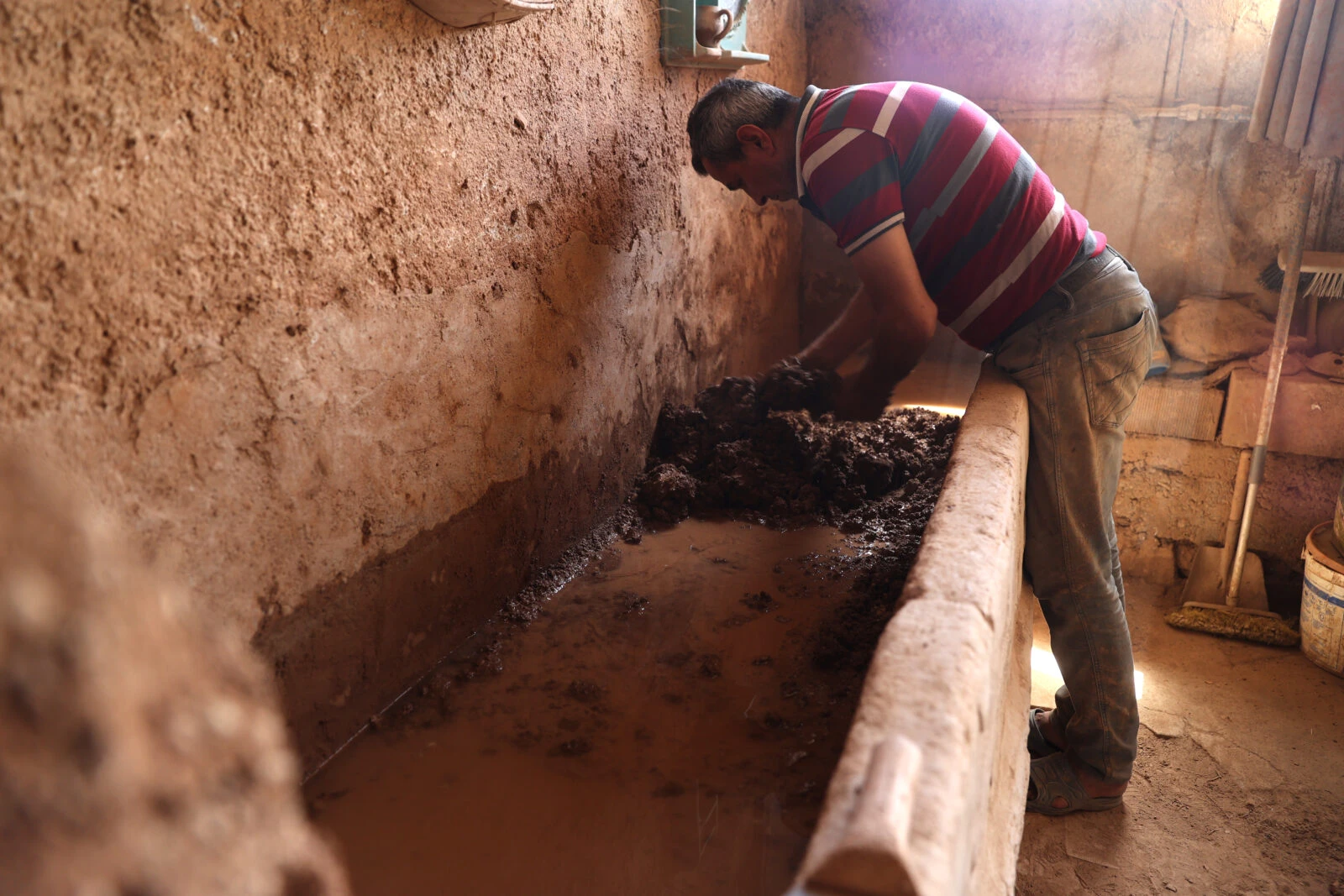
From Avanos to the world
Col’s dedication to traditional pottery has not only preserved a cultural heritage but also attracted a global clientele.
“In the 1980s, there was a shift to plastic. After a while, people returned to using clay products as health problems arose. Here, cheese, water, and casserole pots are made the old-fashioned way and are popular with customers. Clay is brought in by tractor from the mountains, sieved, and turned into pottery clay. After a day’s rest, production begins. The items are left to dry for 3 to 7 days depending on the weather, and then fired at around 800 degrees Celsius. Our products are sold both domestically and internationally, mainly to Saudi Arabia and Germany,” Col explains.
A profession at risk
However, Col is deeply concerned about the future of his beloved craft. “Like every profession, we also struggle to find apprentices. Young people want to work less and earn more. I hope I’m wrong, but our profession might disappear in 10-15 years. There’s a future in this job; you can make anything from clay, but young people don’t work like they used to,” he laments.
As he continues to shape clay with the same passion and precision that defined his youth, Hakan Hakki Col embodies the spirit of Avanos’ pottery tradition. His story is not just about preserving a craft but also about a profound love for an art form that has withstood the test of time. In a rapidly changing world, Col’s dedication serves as a reminder of the enduring value of tradition and the beauty of handmade artistry.
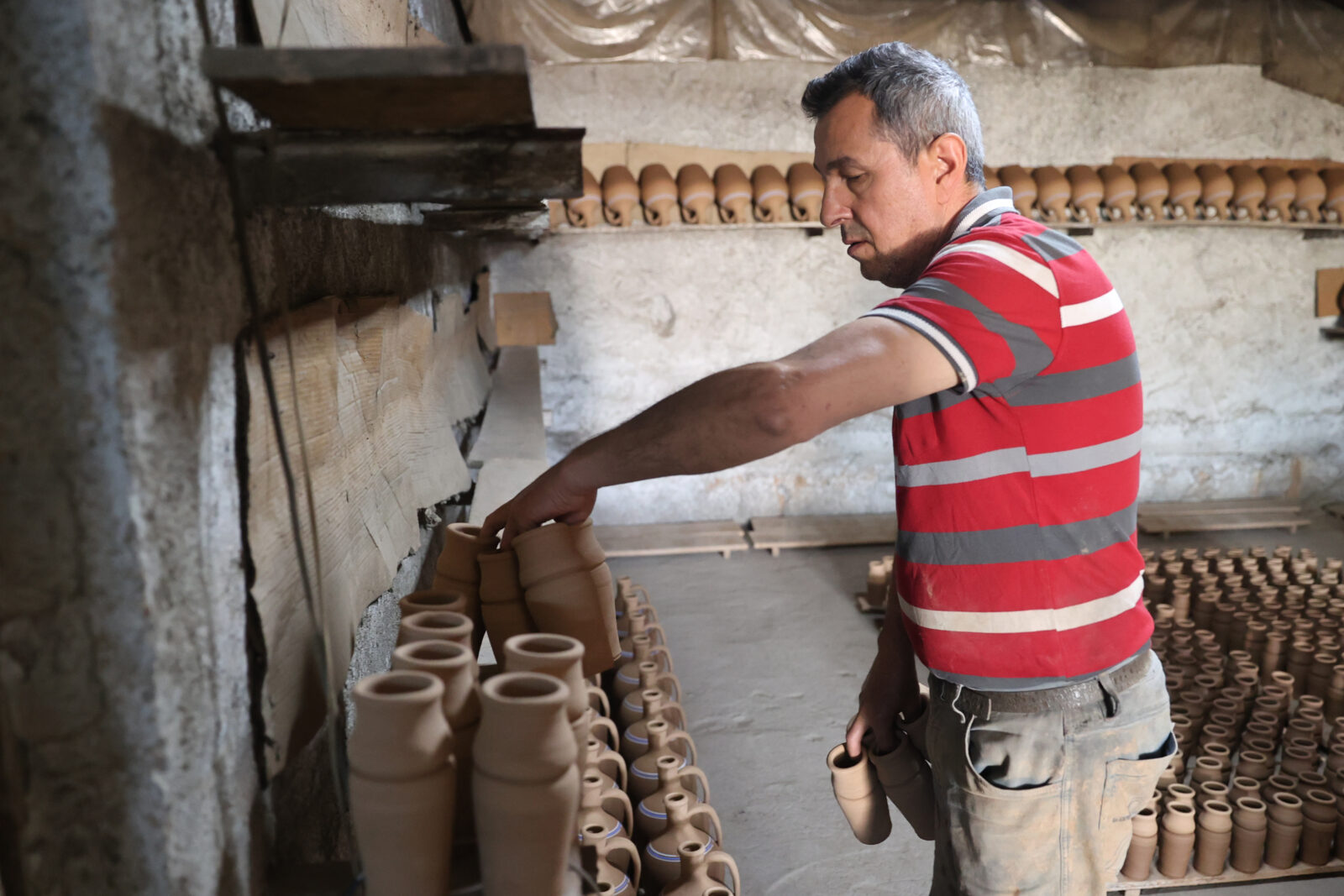
The unique features of Avanos pottery
Nestled among Cappadocia’s tourist hubs, Avanos is famed for its rich, red tuff-laden soil from the Kizilirmak River, fostering a unique pottery tradition. This artistry, dating back to the Hittites around 2,000 B.C., has continued uninterrupted, with Avanos becoming synonymous with high-quality ceramics.
Anciently known as “Venessa,” Avanos’ pottery history spans millennia. Pottery was traded in nearby villages on horse and donkey, a practice continuing into the Ottoman and early Turkish Republic eras.
Pottery artisans traveled routes to trade their wares for essentials like rice, cheese, and salt.
Crafting Avanos pottery
Despite its seemingly simple appearance, crafting Avanos pottery is a meticulous process requiring both skill and creativity:
- Preparing the clay: Soft clay soil from the Avanos mountains and Kizilirmak riverbed is kneaded and left to rest for a week.
- Shaping the clay: Methods include using machines, molds, or the traditional potter’s wheel. The latter involves the potter shaping the clay on a wheel spun by foot, a process taking 4-5 minutes, but painting and finishing can take days.
- Engraving and polishing: Before drying, pots are decorated (engraving) and polished with a metal tool (burnishing).
- Drying: Pots are sun-dried or left in workshop rooms for a day.
- Firing and glazing: Pots are fired at high temperatures and glazed by dipping into a mixture of powdered glaze materials, resulting in a glassy finish.
Visiting Avanos pottery workshops
Avanos is home to many renowned pottery workshops. Notable mentions include Chez Galip with its Guinness World Record-listed Hair Museum, and Guray Pottery, which features the largest rock-carved store and the Cappadocia Underground Ceramic Museum.
Visitors will find a variety of pottery items, from kitchenware like casseroles and pitchers to decorative pieces reflecting Hittite and Phrygian art, including candlesticks, plates, and tear bottles.